3-Part Series
In previous posts, we introduced readers to mass timber technology and some of the hidden benefits of this structural system in our residential development, Bushnell South in downtown Hartford. While we are excited to be using mass timber for the project, we would be remiss in not addressing some of the challenges we encountered in early design phases.
Cost
This structural system comes with a net increase in cost over its conventional counterparts. This increase does consider two items: the reduction of finish materials within the units due to the floor system acting as a finish, and the reduced height of the exterior wall assembly per unit. There are issues that are difficult to quantify in this discussion, such as the potential reduction in schedule due to the increased construction speed, and the potential increase in rents associated with this green technology.
While this technology has been in use for decades other places in the world, one of the driving factors in cost domestically is the relative ‘newness’ of the building system in the U.S. Some contractors even find it cost effective to ship the structural elements from Europe. This is changing. More manufacturing plants are being built to help with demand, and soon we even will have our own manufacturer right here in Connecticut. With Bushnell South, we are lucky to have a client who believes in the mass timber as a sustainable solution, and one willing to commit to the cost increase and longer lead times.
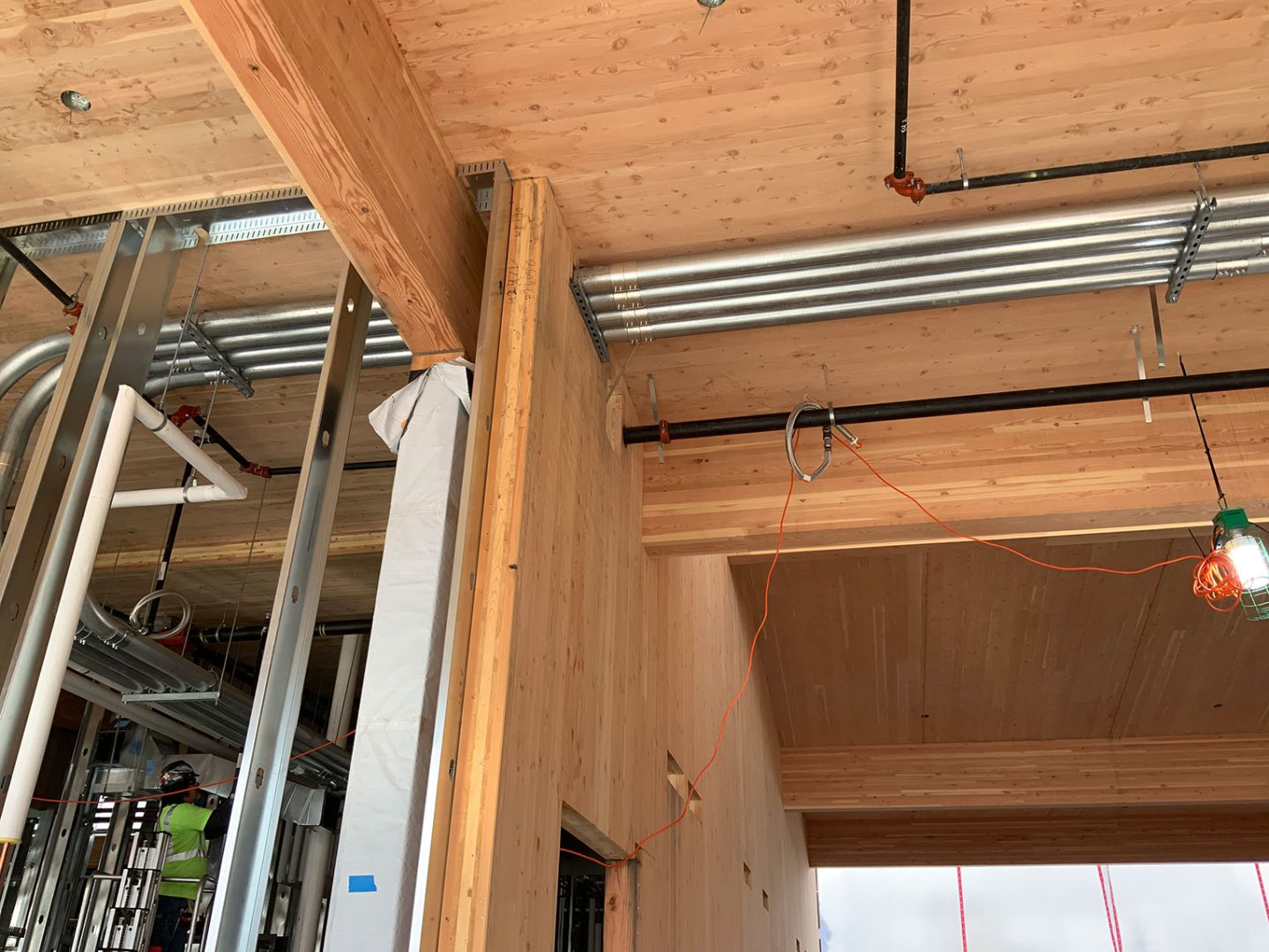
Image courtesy of FFA Architecture + Interiors – Mass Timber: Designing a ‘Completely Wood’ Public Safety Building
Structural Grid
As with any structural system, we are constantly looking to maximize the efficiency of the structure to get the biggest spans for our budget. In this instance, our structural engineer, Rens Hayes from H+O, had already done much of the calculation. The ideal spacing of the structural grid is roughly 16 feet along the length of the building. While this is the most efficient layout for the columns, we adjusted this at Bushnell South to align with our demising walls in the units and take full advantage of the reduced floor-to-floor height. While this works well for one- and two-bedroom apartments, it is very difficult to create a studio apartment within these limits without greatly reducing the efficiency of the structure. In our development, we are lucky to have a second, conventionally framed building to house these studio units. However, this is a consideration if mass timber is the sole construction method.
Mechanical, Electrical, Plumbing
The deep floor assembly of conventionally framed buildings, coupled with open-web wood trusses, leaves plenty of room to run duct work, plumbing and electrical within the units. With CLT slabs, there is zero interstitial space for these systems. This results in additional coordination in both design and construction to achieve the desired results. While we love the look of the exposed wood ceilings, there are spaces where ceilings can be dropped to accommodate duct runs — closets and bathrooms, for example. Side wall sprinkler heads within wall assemblies also clean up exposed piping. The most surprising issue related to electrical and low voltage wiring. In building designs with a more industrial feel, exposed conduit is fine, though the routing should be well documented before construction begins. With Bushnell South, we are designing for a cleaner, more modern aesthetic, which will require the electrical to be fed down from above. There is a minimal amount of ‘interstitial’ space above the CLT slab where we pour gypcrete for sound attenuation; this allows us to run semi-rigid conduit to supply lights and feed electrical into the units.
Final Thoughts
Amenta Emma is fully committed to sustainability, and it is a key factor in how we define a successful design project. Mass timber, cross-laminated timber, and hybrid systems that are now being implemented, help make a difference in the climate impact of our buildings. These systems are not the solution for every building, but as manufacturing continues to evolve and expand, we expect it will become a more integrated part of our building fabric.