3-Part Series
One exciting thing about architecture is the possibilities of evolving technologies and materials. An example is Amenta Emma’s downtown Hartford project – Bushnell South. The project will replace a currently underutilized parking lot in the heart of the city with more than 200 residential units in a mix of rental and ownership models. A key decision made with our client was to utilize “mass timber” for a portion of the buildings.
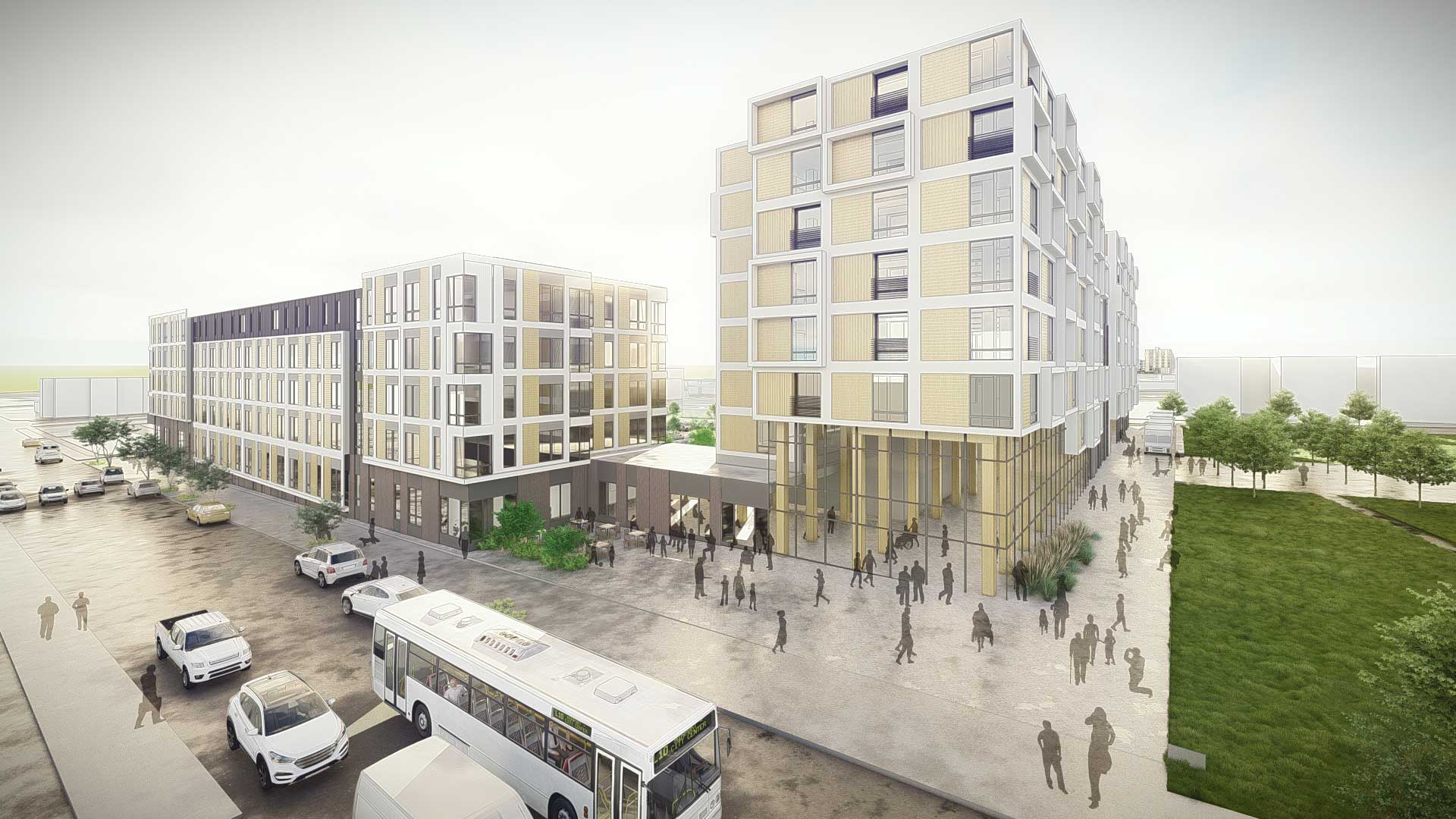
Amenta Emma’s new residential project in downtown Hartford, Bushnell South, is utilizing mass timber technology, a sustainable solution.
Throughout the design process, we consulted with national mass timber experts, worked with local engineers who are well-versed in the new technology, and toured buildings currently under construction to see the framing system at work. We recently shared early concept renderings with the Capital Region Development Authority and addressed several questions and comments from the public about the mass timber construction method.
Can you really build eight stories with wood?
Typically, when we talk wood construction, people imagine homes and small commercial buildings in their neighborhoods. These structures use conventional framing. This process uses wood members with dimensions of just a few inches: 2” x 4” for walls or 2” x 12” for floors. While current technology allows these types of buildings to be five stories, they certainly fall short of our eight-story mark.
In a mass timber building, the dimensional lumber is laminated in a controlled factory environment to yield much larger framing members, 20” x 20” columns for our Bushnell South project. A mass timber building looks more like its steel counterparts, with columns, beams, and floor slabs. These elements are lifted into place with cranes and assembled and bolted together with engineered connections. While our project is eight stories, mass timber currently is being used in buildings up to 25 stories, with even taller projects on the horizon.
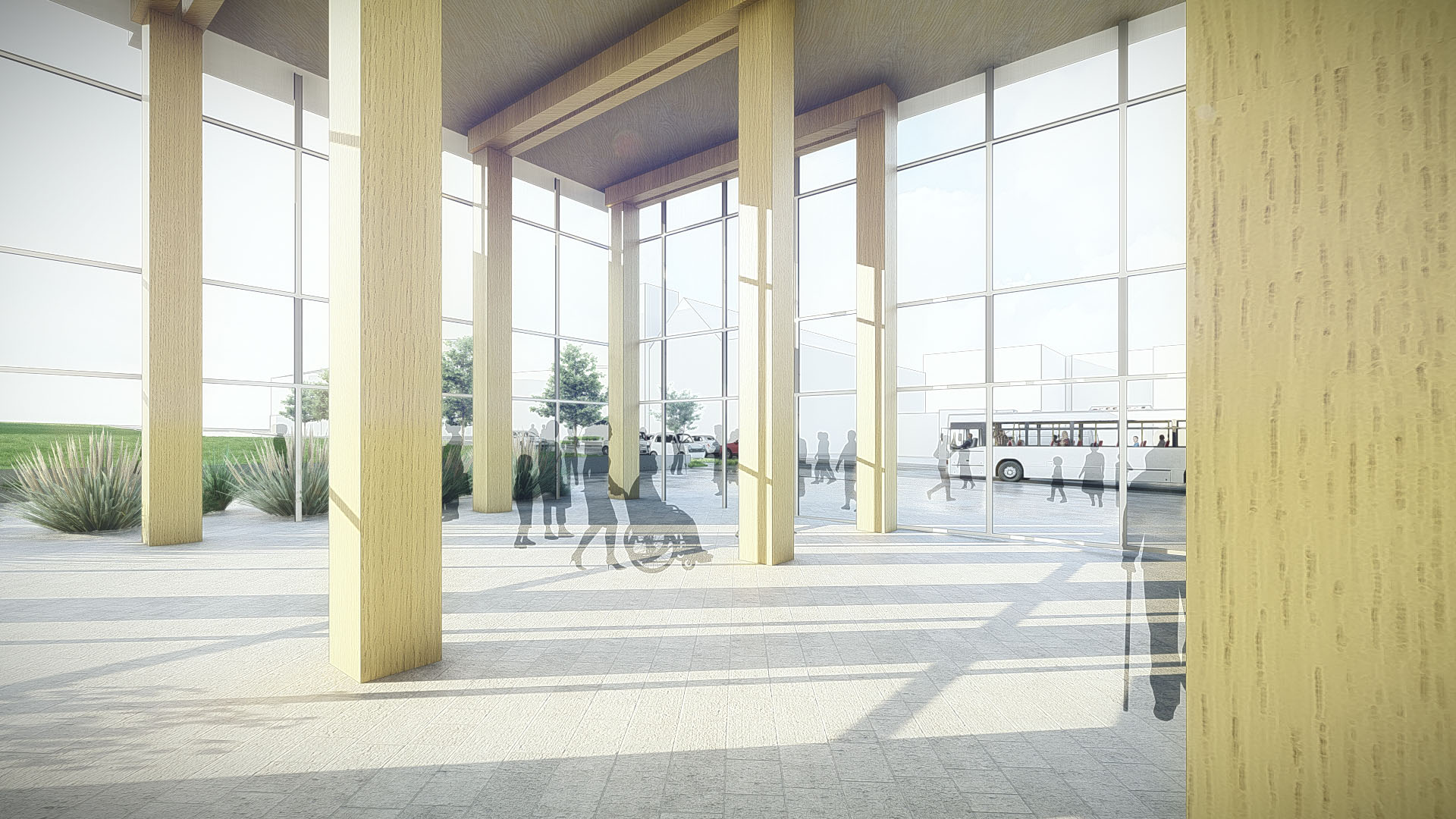
A mass timber building looks more like its steel counterparts, with columns, beams, and floor slabs.
Isn’t wood flammable?
Yes, the wood we use in mass timber buildings is flammable. Our engineers don’t ignore this fact but design for it. They call it charring. Imagine a backyard bonfire; you place a large-diameter log on the fire. The outside of the log quickly burns away, charring the wood fibers as it does. But soon after this outside layer has burned, the speed at which the fire consumes the wood slows considerably. Mass timber structures leverage this property. During a fire, the outer “sacrificial” layers of the large wood columns and beams would char, creating a protective barrier to the structural portion of the column, thus giving occupants plenty of time to exit the building.
Why not just use concrete and steel?
While there are many good answers, the most compelling is sustainability. Construction materials account for nine percent of global greenhouse gas emissions, according to recent studies, and most of these emissions come from steel and concrete. Conversely, the trees from which mass timber is made, store carbon dioxide, resulting in a reduction of the carbon footprint of our building by up to 40 percent. When we combine this structural system with a high-performance building envelope, we will achieve reductions in our heating and cooling demand and deliver a more sustainable project.
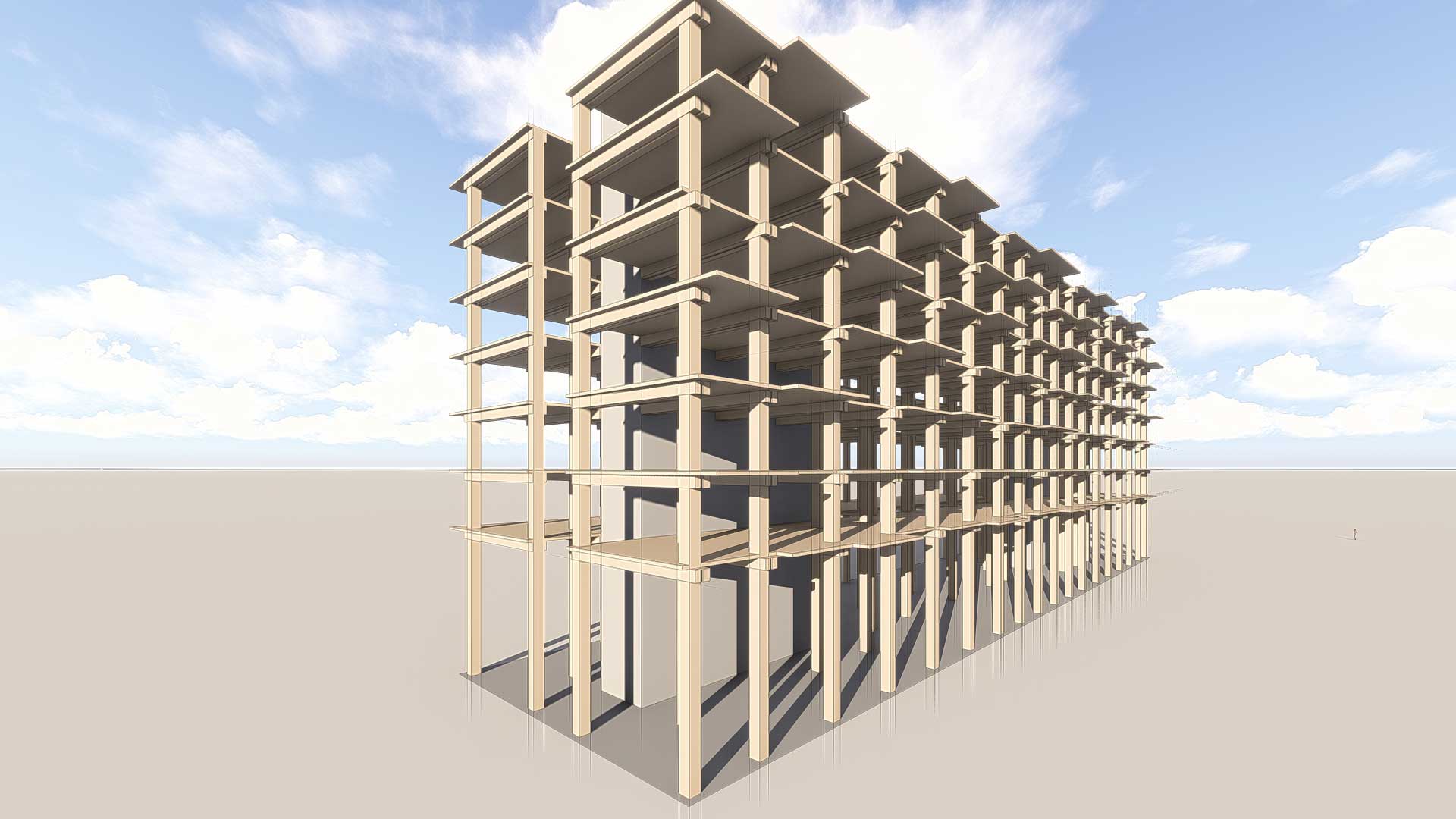
The Bushnell South project is eight stories tall. Mass timber currently is being used in buildings up to 25 stories.
Mass timber, mixed with CLT, isn’t for all buildings. However, given its scale and urban setting, we saw the Bushnell South Development as an ideal project to leverage the benefits of this sustainable technology. We are excited to have a client and project that emphasizes our commitment to design and sustainability.